Waste Heat Based Evaporation System
Waste Heat based Evaporation System
Industrial processes like Reverse Osmosis plant generate liquid effluent containing a high amount of inorganic soluble salts. Conventionally, wastewater containing high soluble impurities (dissolved solids) cannot be disposed of to water bodies. Methodologies followed are
- Conventional methods employ the high dissolved solids effluent is mixed with other dilute wastewater streams, before disposal, to meet disposal standards.
- In many cases, the soluble impurities are precipitated by using chemicals.
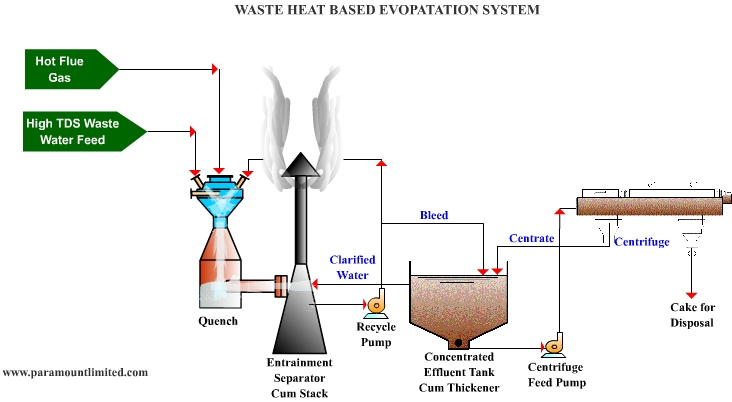
To achieve the concept of “zero discharge”, the wastewater with high dissolved solids is treated using evaporator / RO technology where the liquid fraction of the wastewater is recovered in the form of water, which may be reused, and impurities present in the wastewater are collected separately as inert solids/ concentrate. Even though the evaporation/ RO technology provides a proven remedy for treatment of wastewater with high dissolved solids, it is used on a limited scale because of:
• High cost of equipment
• High cost of energy for its operation
• Complex operation requiring skilled manpower and major plant automation
Paramount provides an innovative concept of using “Quench”, a proprietary compact design for evaporating water from wastewater containing a high level of dissolved solids (50,000-55,000 ppm). This concept works to optimize and utilize the waste heat of the flue gases generated from the power plant/ incinerator units.
In normal practice, a quench is used to cool the hot gas by having a direct contact water spray to reduce the gas temperature. Water is evaporated and converted to steam. This concept is based on evaporative cooling. The gas is further treated, as the case may be, depending upon the process. This concept of evaporative cooling is utilized from a different perspective (i.e. to evaporate the water using the waste heat rather than the conventional concept of cooling the gases with water).
This would result in the concentration of wastewater in the form of the slurry, containing suspended solids, generated due to the presence of high TDS and evaporation of water, which can be centrifuged to form a disposable cake. The centrate from the centrifuge is sent back to the quenching system for further evaporation. The cooled flue gases with water vapours can be discharged to the atmosphere through a stack.
This innovative concept was also presented to the Ministry of Environment and Forest (MOEF) and has been accepted.
This approach also helps to achieve a reduction in the initial cost of the plant including extremely low operating cost.
Comparison of Waste heat based Evaporator System with conventional Evaporator (Multiple effect) systems:
Sr. No. | Features | Evaporator System | Quench System |
1 | Type of System | Multiple Effect Evaporator using steam as source of Heat | Flue Gas Quenching System to evaporate the water using waste heat in flue gases |
2 | Type of Operation | Complicated operation as it requires operation of lot of pumps, reactors and is highly instrumented | Very simple to operate as only four simple equipment needs operation |
3 | Operating Personal Requirement | Highly skilled operating staff conversant with process plant operation | Skilled operating staff with normal operating skills |
4 | Flexibility W.R.T. To Turn Down and Change in Effluent Characteristics | Less flexibility as the plant requires lot of controls due to change in effluent characteristics and turn down | No change in plant operating parameters are required even if there is a major change in plant capacity and effluent characteristics |
5 | Flue Requirement | Envisages Installations of a new Boiler for meeting system’s steam requirement which would use fuel for steam production | Steam Boiler is not required and hence does not envisage burning of fuel |
6 | Reliability W.R.T. | Good | Very High |
7 | Turn Down Possible | Up to 30% max. | As low as 10% |
8 | Power requirement | 15 – 17 KW/M3 | 1.5 – 1.6 KW/M3 |
9 | Steam Requirement | 300 – 350 kgs/m3 | Not required |
10 | Cooling Water Requirement | Yes | No |
11 | Space Requirement | More | Less |
12 | Quality of End Product (Cake) Generated | Cake with 75 – 80% solids | Comparable |
13 | Any other Salient Feature | High Maintenance Cost due to cleaning requirement of scales formed on tubes | Very low maintenance cost due to less number of equipment which are simple to operate and does not require de-scaling |
Contact Us At
Address
Paramount Limited, Paramount Complex, Near Natubhai Circle, Race Course, Vadodara, Gujarat - 390007
Phone Number
Vadodara: +91-0265-2397111 (7 lines)
New Delhi: +91-11-26186525, 26186369
Mumbai: +91-22-24073108, 24078105
Email Address
Vadodara: sales@paramountlimited.com
New Delhi: delhi@paramountlimited.com
Mumbai: mumbai@paramountlimited.com